Pumping Equipment
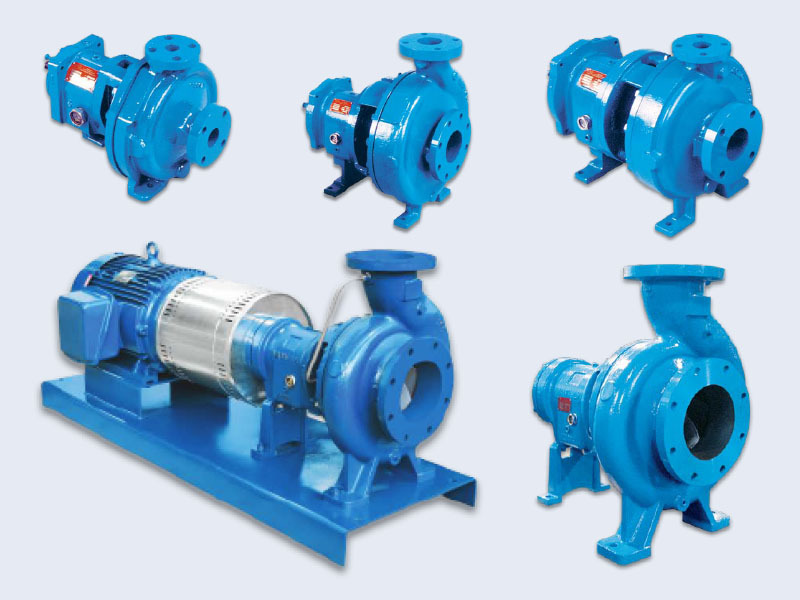
ANSI Process Pumps
The gold standard for chemical process pumps. All ANSI pumps are built to meet the same standards and dimensions. This means that getting parts and service for ANSI pumps is easier than for some other styles of end suction centrifugal pumps. Used predominately in the chemical, food/beverage, pulp & paper, and oil & gas industries for moving water and chemicals.
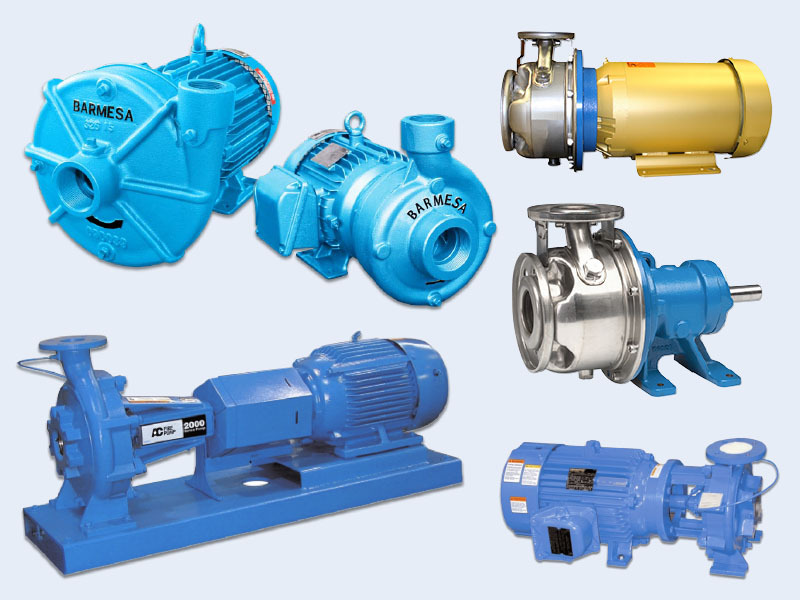
End-Suction Centrifugal Pumps
Centrifugal pumps can transfer large volumes of fluid by transferring kinetic energy using a rotating impeller. Centrifugal pumps are the most common type of pump in use today and give users the ability to transfer large volumes of fluids at low to medium pressure. Common in all industries.
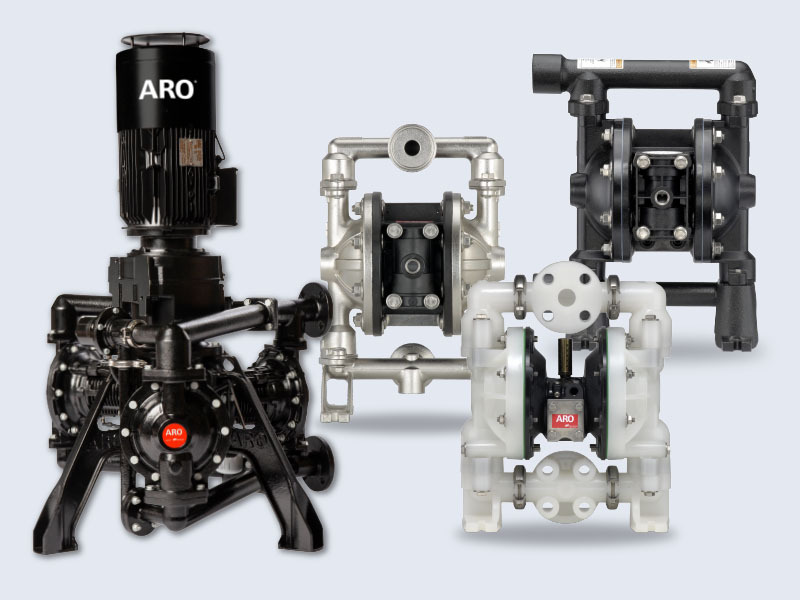
Diaphragm Pumps
Diaphragm pumps are positive displacement pumps that use an elastomeric diaphragm and valve system to move fluid. Diaphragm pumps are self-priming, can be fully submerged in liquid, and come in a wide variety of materials. This makes diaphragm pumps one of the most versatile options on the market. They are most commonly air operated, making them intrinsically safe, but are also available in electrically driven models for added efficiency.
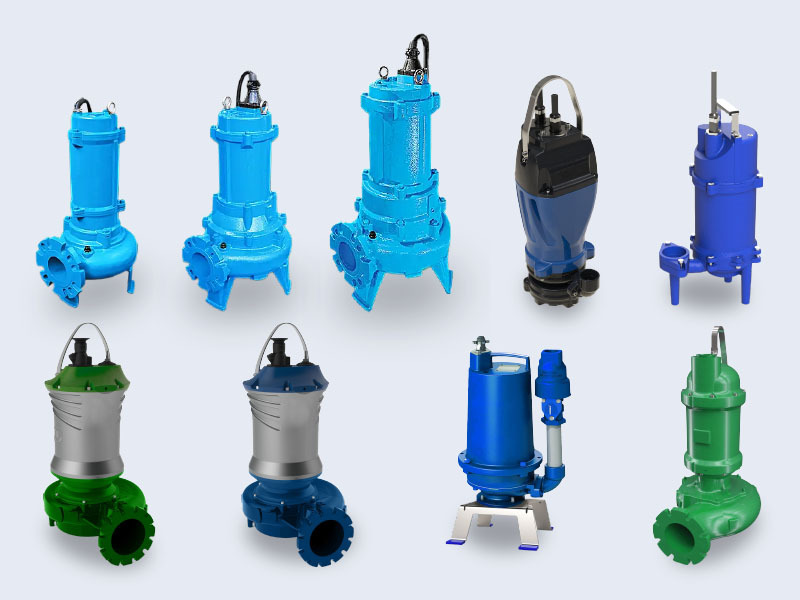
Grinder/Chopper Pumps
Grinder and chopper style pumps are designed for applications with stringy or difficult solids. This style of pump is mostly commonly submerged in the pumping liquid, but is also available in vertical and horizontal end suction styles. Chopper pumps originated in the agriculture industry, where chicken feathers were clogging pumping systems, and are also commonly used in wastewater and sewage treatment, food processing, seafood, and pulp & paper applications.
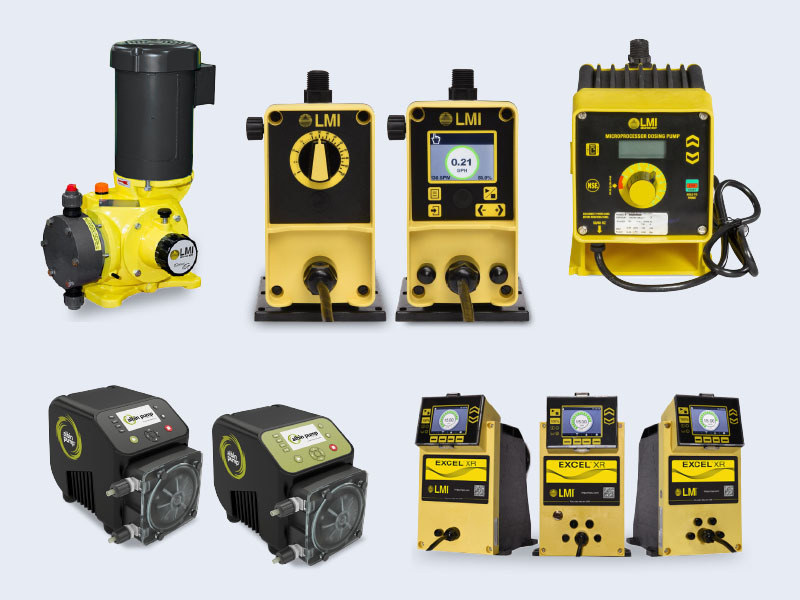
Metering Pumps
Metering pumps are designed to deliver an accurate and consistent amount of fluid to an application, making them ideal for applications where exact fluid volume is critical. These pumps are available in a variety of different pumping technologies, including peristaltic, diaphragm, and progressive cavity. Commonly used to control pH in industrial and wastewater applications.
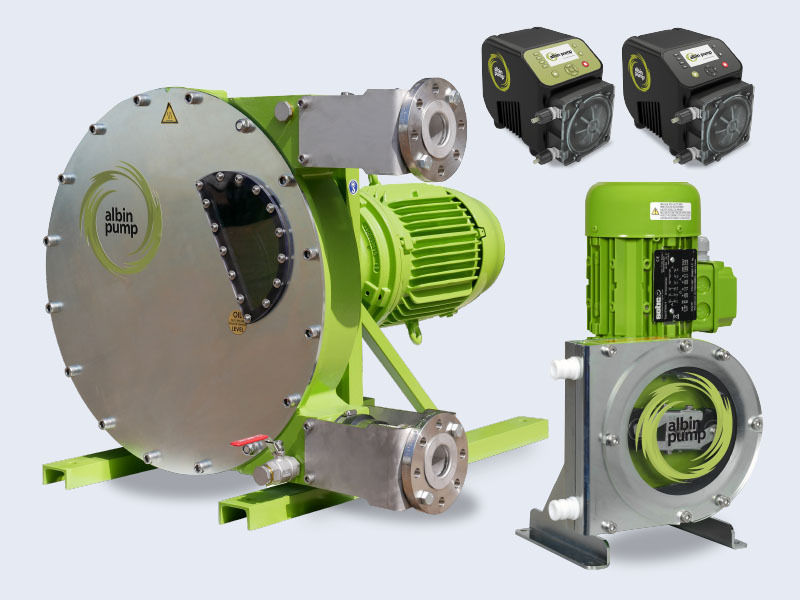
Peristaltic Pumps
Peristaltic pumps operate using the principle of peristalsis. Rotating rollers, or shoes, compress and relax a flexible hose, forcing the fluid through the hose as the shoes rotate. Peristaltic pumps are low shear for delicate fluids and fluids containing solids. It is also a technology with zero slip, meaning these pumps provide accurate and repeatable volumetric flows and they are good for abrasive applications.
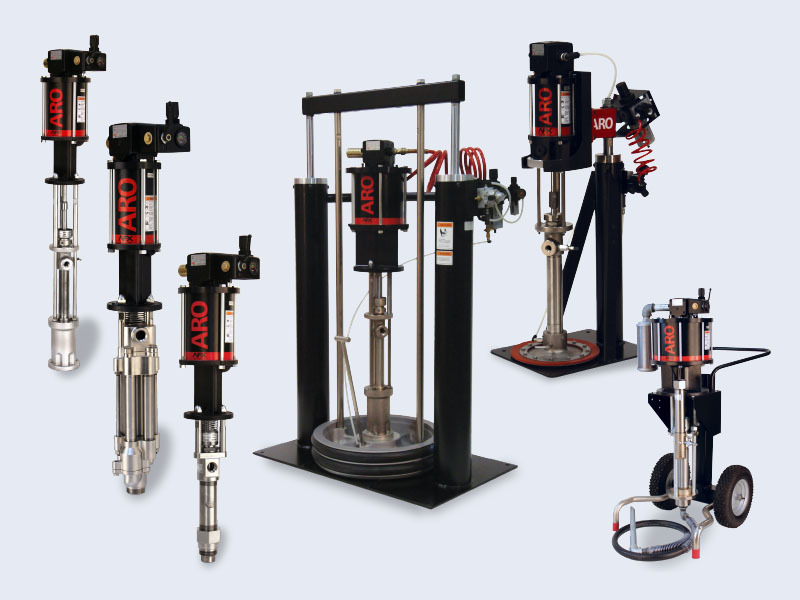
Piston Pumps
Piston pumps use a reciprocating piston to move fluids. They are typically used for applications with high pressure, high viscosity, and low flow. Common applications include oil, grease, paint, glue, and sealants.
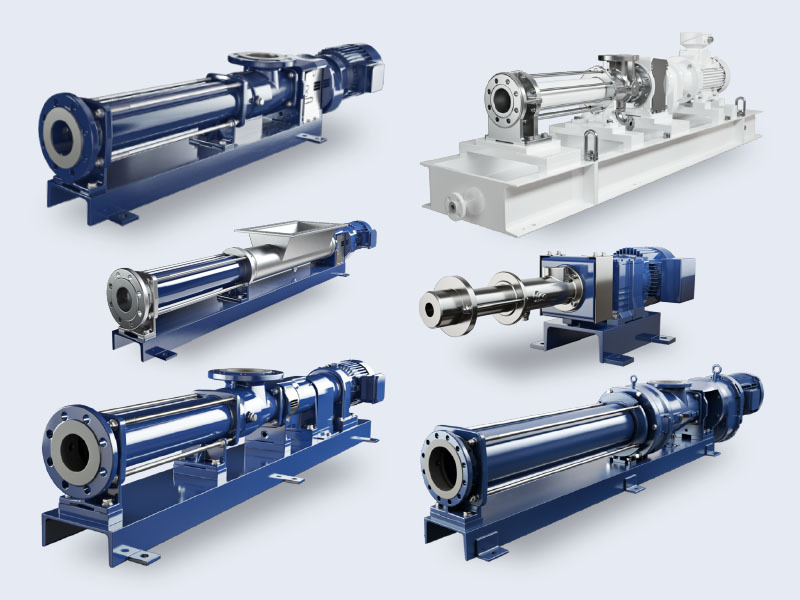
Progressive Cavity Pumps
Progressive cavity pumps are positive displacement pumps that use a helical rotor and a stationary elastomeric stator to move fluid. As the rotor rotates, the cavities between the rotor and stator progress from the suction side to the discharge side of the pump. Progressive cavity pumps are ideally suited for applications with abrasives, high solids content, or where precise flow is required.
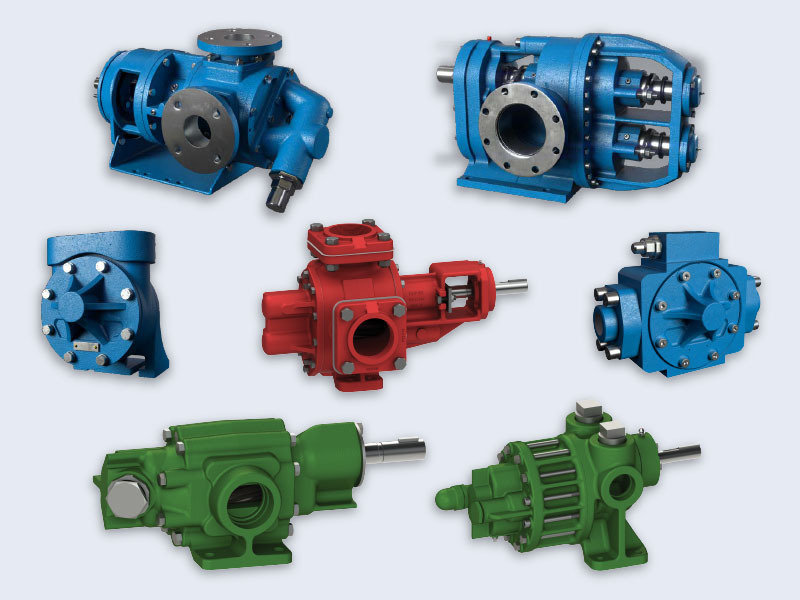
Rotary Gear Pumps
Rotary gear pumps are positive displacement pumps that use two (or more) intermeshing gears to move fluids. Gear pumps are simple, reliable, and efficient and are ideally suited for low to medium viscosity, high lubricity, clean fluid applications such as oil or fuel transfer.
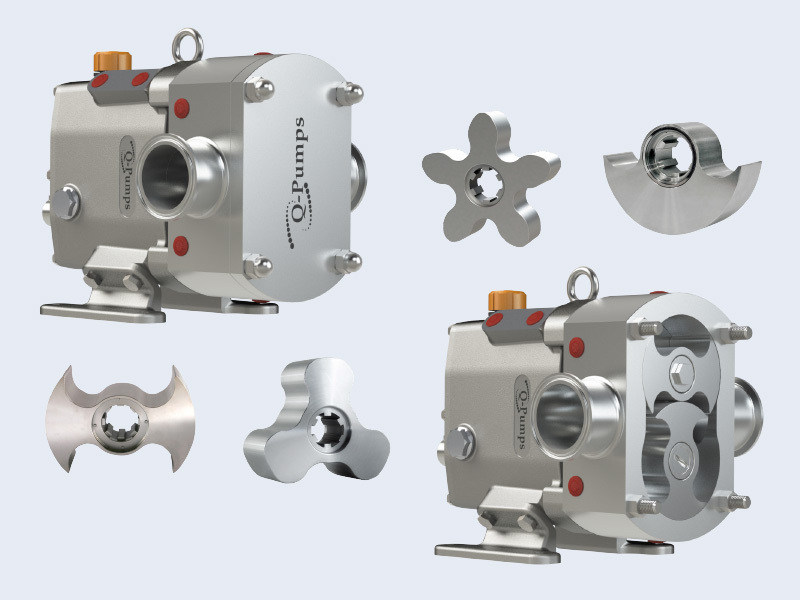
Rotary Lobe Pumps
Rotary lobe pumps are positive displacement pumps that use two rotating lobes to move fluids. Rotary lobe pumps operate using similar principles to a rotary gear pump. However, the lobe design allows this style of pump to handle solids and abrasives and provide low shear pumping. This makes this an ideal choice for food, beverage, and pharmaceutical applications.
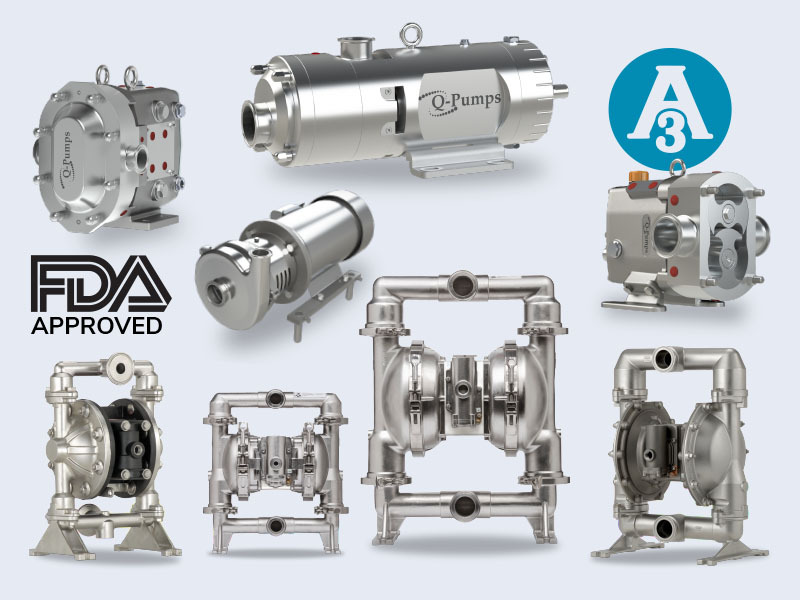
Sanitary Pumps
Sanitary pumps, using a variety of pumping technologies, are specifically designed for use in industries where cleanliness and hygiene are imperative. These pumps meet strict sanitary requirements with the materials that are used for each component of the pump and for the design of the pump. These pumps typically come with food- or pharmaceutical-grade materials and surface finishes and often times are designed to clean-in-place or sanitize in place.

Self-Priming Pumps
Whereas many pumps require being located below the surface of the pumping fluid, or to be primed manually, self-priming pumps offer users the ability to locate their pump above the surface of the pumping fluid. This makes servicing a pump easier than a submersible pump but allows for a more flexible installation location. Self-priming pumps are available as centrifugal pumps, where an external casing and check valve allow the pump to pull vacuum to draw fluid into the pump, and are also a feature on certain positive displacement pumps including diaphragm and vane pumps.
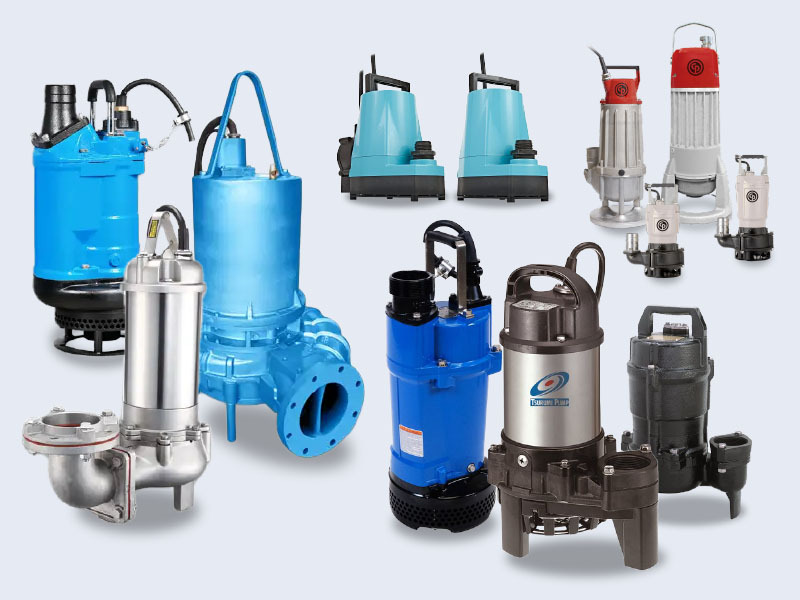
Submersible Pumps
Submersible pumps allow users to submerge the entire pump and motor in the fluid being pumped. This makes pumping significantly more convenient in applications such as wells, sumps, construction sites, and mines. This style of pump can be outfitted with float switches and controls so that the pump automatically turns on when certain levels are reached.
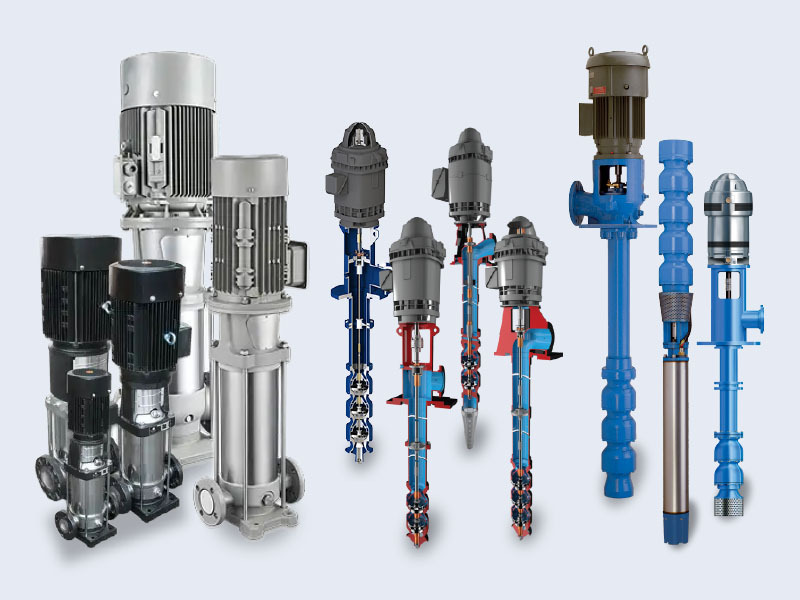
Vertical Turbine Pumps
Vertical turbine pumps are a type of centrifugal pump designed for applications below ground level. This style of pump is well suited for deep water wells, reservoirs, and large tanks. The pump consists of a vertical shaft with multiple impellers arranged in series on the shaft to meet the required pressure. A line shaft and column pipe connect a discharge head and motor to the pump, or bowl assembly. Motors are typically at ground level and pumps are typically below ground level. This style of pump is typically bespoke to each application and can accommodate high flows and high pressures.